A new workforce is emerging, and with it, a new way of working. As new employees enter the field, and others retire, a knowledge gap develops between these generations.
The importance of knowledge transfer in manufacturing
A new workforce is emerging, and with it, a new way of working. As new employees enter the field, and others retire, a knowledge gap develops between these generations. Anticipating and preparing for potential interruptions to your production is crucial, and finding the means to capture and instill essential manufacturing skills and critical expertise is at the forefront of many companies’ goals. The effective transfer of knowledge to new employees, and cross-training existing employees, has become essential to maintain productivity, efficiency and innovation, and increase agility and adaptability.
The 2020 pandemic accelerated the need to capture knowledge as many companies experienced a reduction in their workforce and a corresponding loss of skills and knowledge. At the same time, the pandemic highlighted the effectiveness of digitally mediated human-human and human-computer interaction. “Even though training and re-training is part of day to day manufacturing operations, the post COVID-19 restart underlined the toll it takes both in time and productivity,” notes Csaba Szabo, executive director of business development and global partnerships at SRI. “Having a repository of instantly accessible training materials that not only highlight the way things should be done, but also the underlying principles and knowledge of why it’s done that way can result in significant productivity gains.”
It is important to understand the types of knowledge that can be effectively transferred. Explicit knowledge is documented objectively, preserved in manuals, documents, videos, etc. In contrast, implicit knowledge is more nuanced; it arises from experience and is difficult to communicate directly. This kind of knowledge might be thought or sensed rather than documented in writing. For example, an expert may identify problems or malfunctions from something as subtle as the sound a machine is making.
Both types of knowledge need a mechanism through which information Is captured, analyzed and finally, efficiently and effectively transferred to other employees.
The promise of knowledge transfer using AI
The traditional method of transferring knowledge is through the use of manuals, videos or in-person training. There are many disadvantages to these conventional methods: large manuals are difficult to search and update, videos are limited by angles and editing, and in-person training is labor-intensive and expensive. And most importantly, these methods work best for explicit knowledge but are less effective at capturing implicit knowledge.
SRI has developed a system that uses AI (artificial intelligence) to capture both implicit and explicit knowledge. This is done by gathering data from an array of sensors and analyzing this data with AI. The result is an indexed and searchable knowledge base that uses a variety of techniques to transfer knowledge. The result is a comprehensive method for extracting the knowledge of an experienced operator. To achieve this, SRI developed an AI-enabled ecosystem for knowledge transfer, consisting of three components:
- AI analytics: AI analytics map the raw sensor data into a coherent model of what is happening as experienced workers perform their tasks.
- Augmented input: The resulting analysis is supplemented with structured interviews and walk-throughs.
- Cross-referenced insights using AI: Finally, the knowledge is enhanced using additional AI capabilities, which analyzes the data to look for key “nuggets” of information. These are then cross-referenced with the knowledge base, leading to further insights.
How SRI AI technology captures knowledge
Companies large and small with varying production demands and skillsets can benefit from SRI's method of knowledge capture through AI. The process begins with building a database for the transfer. Video, body cameras and other sensors register position, motion, and sounds from operators and machines. Additional sensors may be added to the machine to record data regarding its state at various times.
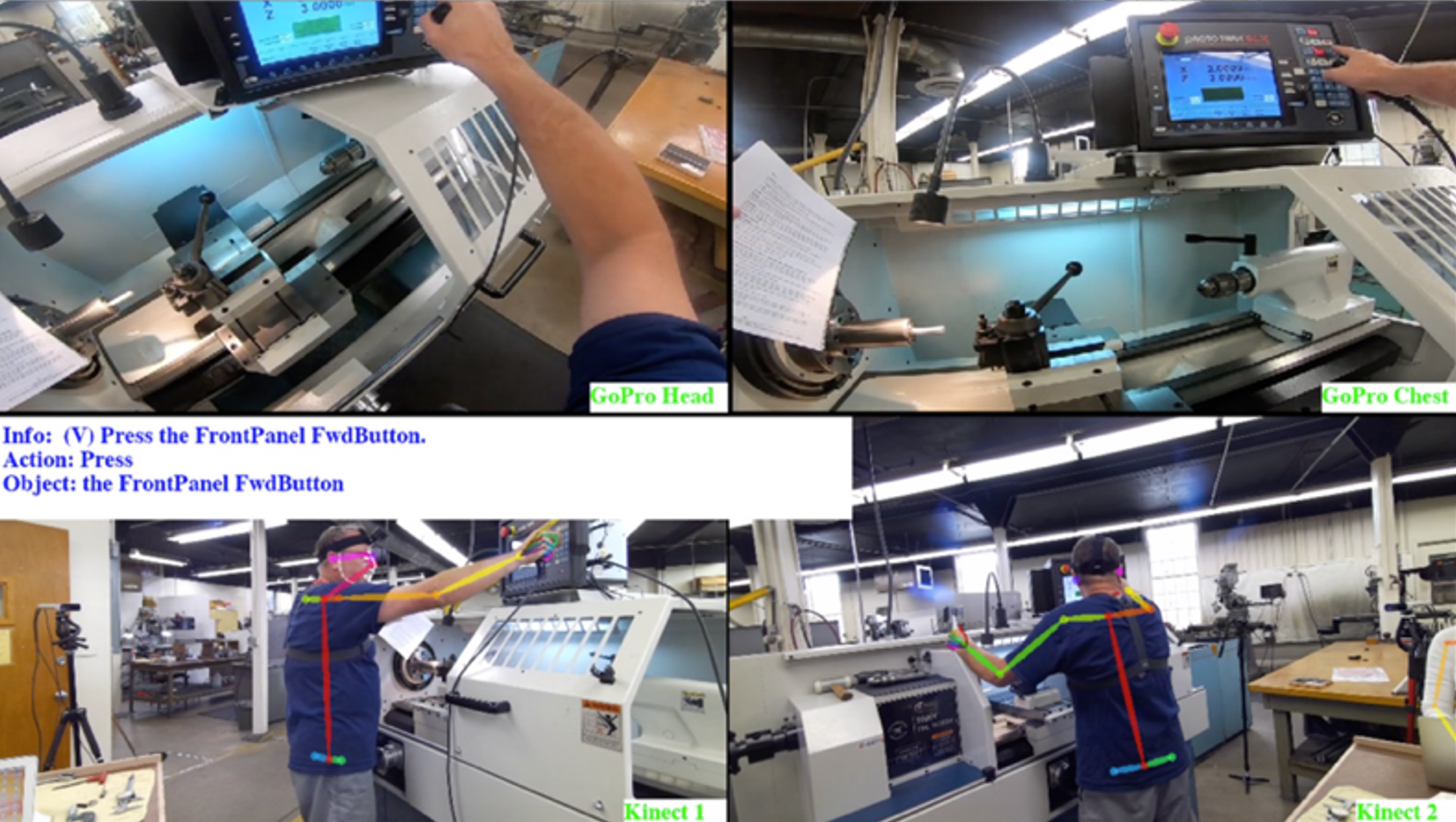
The data is then consolidated into human-understandable knowledge using deep learning-based methods that detect the objects in the scene, assess the operator's pose, hand movement and movement of instruments. Deep learning is also used to understand the text in manuals and the sounds in the environment, including machine sounds and the operator’s speech. Combining the different kinds of analytics enables deeper understanding. For example, if speech recognition detects an unknown word (perhaps vocabulary that is specific to a task or to a particular factory floor), associating it with the visually-detected activity in progress can suggest the meaning.
The result is a knowledge base that indexes the knowledge in a form that is readily usable by multiple training techniques.
Adaptable training that goes where you need it
Training can be both off- and online, in any formfactor and any time segments that the company requires. The knowledge base can also be used to assess employees' skills and give meaningful feedback in skills training.
For example, the knowledge base can be used to support:
- Fine-grained search, e.g., "show me where the micrometer is used" to enable employees to easily find the specific information they need to perform a task.
- Customized training materials for just-in-time (JIT) or online and offline instructional courses.
- Augmented reality (AR), e.g., to project a virtual schematic onto a physical circuit board to help an employee understand the layout of the circuit. AR can also be animated to show a sequence of actions, e.g., showing how a machine is to be serviced.
In real-world manufacturing, trainees are often using both hands, so AR can be combined with conversational intelligence, provided by SRI's natural language processing (NLP) technology, allowing them to ask questions while using AR. Deploying an AR solution can also have a substantial impact on remote areas or for small businesses that may not have extended support in training or information technology.
Further uses of SRI AI technology
SRI is a world-renowned supplier of AI-enabled technologies for manufacturing. As well as knowledge capture and transfer, SRI supplies technologies that are augmented by artificial intelligence, such as:
- mobile autonomous robots for factory environments
- adaptable manipulation of manufacturing environments
- anomaly and fault detection in machines
SRI has been working with Japanese automotive manufacturing companies to capture traditional craftmanship knowledge of the industry. “By leveraging next-generation AI capabilities, we can observe each movement and measure the exact output to be able to re-train a novice worker and thus enable them to perform at the level of the best workers,” notes Szabo.
The current manufacturing environment is well-poised to capture knowledge with AI. With an emerging workforce and the lasting effects around the world due to the pandemic, minimizing interruptions to your production and maintaining valuable skillsets is vital.
“The next big productivity gains will yield from augmenting human work with AI capabilities. One example is capturing expert knowledge, both implicit and explicit, and making it readily available via an easily searchable ‘YouTube-style’ training platform,” says Szabo. “This not only would increase the overall flexibility of all manufacturing capabilities, but also decrease downtime due to training.”
Interested to learn more? Head to www.sri.com.
SRI recently held a webinar for the Japanese manufacturing industry. View the full video presentation by Bill Mark, President of SRI's Information and Computing Sciences division, which includes a working demonstration of our AI knowledge capture technology in action.