Industry expert Ray Karadayi walks us through some of the incredible ways in which Smart Machining is revolutionizing On-Machine Metrology
Achieving Smart Machining with On-Machine Metrology
Data is the lifeblood of every production facility. Design data works with machining center controllers to precisely create part features on multi-axis equipment that meet stringent customer and industry standards. Inspection and metrology data confirm part features meet these standards and are used to adjust the process and equipment to keep this the case. This all takes place in a changing, dynamic machining environment. Machining creates friction, which creates heat and vibration. Tools wear. Accuracy wanders. Measurement data therefore becomes the guardian of the process for confirming good parts.
It has become a generalized belief that good measurements must be achieved in a clean and static quality department on coordinate measuring machines (CMMs). The production equipment and environment is just too noisy and dirty.
This is not the case. Capturing metrology data on machine tools where parts are made creates a singular opportunity for using that data to identify machine-based changes as they occur and adjust them in real time. The results are more good parts per shift, longer-lasting machines and tools, and the ability to share data throughout the factory—all significant production advantages on equipment you already own. This is the definition of Smart Machining.
My company, Applied Automation Technologies (AAT3D.com), is an R&D-oriented metrology software company with more than 30 years of success in developing software that improves manufacturing quality. Our flagship product is CAPPSNC, (Computer-Aided Part-Programming System), an advanced measurement software system that enables something that decades ago would have sounded like a pipe dream: It allows CNC machine tools to perform part measurements like a CMM.
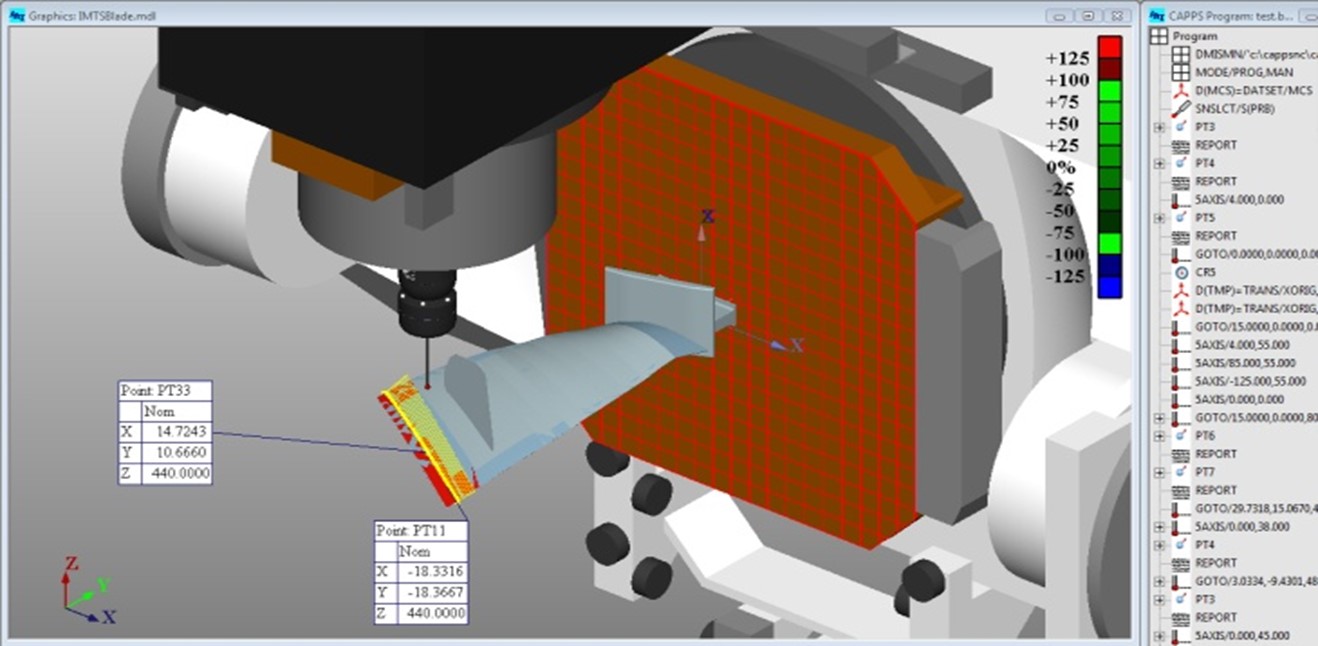
From CMM to CNC
Manufacturing companies measure parts for three straightforward reasons:
- To avoid releasing any bad parts to customers
- To maintain quality control procedures that produce good parts
- To create SPC (statistical process control) processes that maintain and improve the manufacture of good parts
External CMMs have become faster and more accurate over time, but necessitate removing apart from production equipment, fixturing it in a CMM, and, when necessary, returning the part to production equipment for further work. These steps take time and introduce new opportunities for human or automation equipment error to creep in. This remains true even though some CMMs themselves have become smaller and portable enough to be located adjacent to the machining center. The history of modern metrology can in a sense be seen as tracking the movement of part measurement from distant metrology equipment to as close as possible to the production equipment —culminating with the ability to measure the part on the equipment making it.
Another method of measurement is the use of dedicated gages that can quickly collect measurement data directly on the shop floor. These gages provide measurement data at high rates and are very effective for high-volume production. The disadvantage is their lack of flexibility: Designed for a single part, they are expensive to maintain or modify.
In contrast, the CAPPSNC on-machine measurement system provides capabilities to quickly develop measurement programs offline and run these programs directly on CNC machine tools in a similar fashion to a CMM. Offline programming with virtual machine models and the use of CAD part models allow the machine tool itself to be programmed to perform complex measurement and reporting tasks, including multi-datum profile and true position analysis.
Users taking advantage of these programs with our work off set option are no longer restricted to using standard macros, or indicators to identify only the most basic geometry as machining coordinate locations. Using CAPPSNC alignments, complex 3D features, intersections, tooling balls, and best-fit alignments are used to pick up work offsets. Part setups are both faster and more accurate, saving time, improving the distribution of material removal, and saving money.
Realistic program simulations, collision avoidance, and optimum measurement path generation for multiple geometric features makes it very easy to program and flexible to make changes for any type of machine-tool configuration. This ultimately enables a very easy method of quickly generating metrology data directly at the production source.
CAPPSNC– Software and Hardware
The CAPPSNC system connects with the machine tool with an ethernet cable and can read and write to any controller parameter. The system employs durable, accurate probing systems provided from companies such as Marposs, Renishaw, BLUM, M&H, and Heidenhain. Probes are loaded automatically like a cutting tool and are designed to minimize the effect of vibration, acceleration, coolant exposure, and possible collisions.
CAPPSNC creates dedicated probe calibration routines to achieve maximum accuracy. Calibration eliminates probe lobbing (triggering) errors in order to measure points along3D vectors. Compensation data is created for each point at its measuring velocity. The software calculates probe offsets and runout instead of trying to force the probes to be perfectly straight. The result is a partner relationship between probes and cutting tools that provides feedback for tool-error detections.
Tactile probes are not the only measurement method enabled by CAPPSNC: Since 2014, accurate and repeatable non-contact laser scanning has also been part of the on-machine measurement arsenal.
_____________________________________________________________________
Capturing metrology data on machine tools where parts are made creates a singular opportunity to identify machine-based changes as they occur and adjust them in real time. The results are more good parts per shift, longer-lasting machines and tools, and the ability to share data throughout the factory, all on equipment you already own. This is Smart Machining.
______________________________________________
The Goal: Immediate, Ongoing Process Improvement
The data generated with CAPPSNC’s on-machine measurements is not only valuable for part verification—the goal here is not to make stand-alone CNNs obsolete. Rather, it’s to use the data—immediately, as soon as it is generated—to improve the machining process by adjusting various machining parameters such as work offsets and tool offsets.
One reason it can do so is because the CAPPSNC system works as a variation of Edge Computing: The data need not travel away from where it is generated in order to be processed and used to improve machining quality. In fact, it’s a secure closed-loop system — everything happens on the machine tool and its controller. What really makes the software powerful is its ability to convert the calculated metrology data it collects into machining parameters and directly update the controller. It runs outside the machine tool controller yet works as part of the machining process.
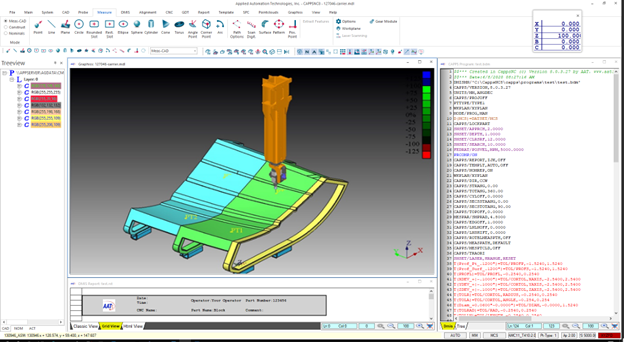
Contrast this with the use of a standalone CMM, which traditionally measures parts made on a number of different machine tools. When that CMM catches an out-of-spec part, an extra level of complexity is needed to trace the part back to the machine that made it and perhaps use the data to diagnose the machine.
But the CAPPSNC on-machine metrology system serves a single master—the machine tool itself: Error detection, diagnosis, and compensation all happen where the error occurred—and quickly. Periodic health checks throughout each shift enable greater machine consistency, which yields more good parts, which lowers production costs while improving throughput. Networking such Smart Machining data throughout a facility makes such improvements possible on all your production equipment.
Inconclusion, it remains important to remember a few facts about collecting on-machine metrology:
- The goal of machine tool probing is NOT to eliminate CMM part verification.
- The goal of on-machine metrology is to improve manufacturing processes
- Programs can be short; measuring and immediately correcting for critical errors
- Proper implementation will minimize many loops with CMMs
- Where it may be impossible or very expensive to move parts to a CMM; i.e. for large die and molds or aerospace components, on-machine metrology provides a qualitative and affordable solution.
Want to see more? Check out Ray's white paper on Smart Machining in Metrology - available only to subscribers.