An informative conversation with SICK AG's Production Manager from within their 4.0 NOW factory
Conversation with SICK AG’s Production Manager at the 4.0 NOW Factory
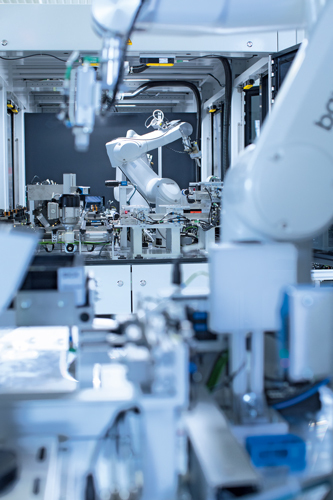
In Freiburg, Germany, the gates to SICK’s 4.0 NOW factory opened for the first time in 2019. Since then, groups of visitors gained exciting insights into the intricacies of production there. Joachim Schultis, Head of Operations Photoelectric Sensors & Fibers, was given a grand tour on the capabilities of the factory itself. In this interview, Schultis expands on what he has learned from operating an Industry 4.0 factory.
Q: As the Production Manager in a factory operating on Industry 4.0 principles, how do your tasks differ from those of a Production Manager in a conventional factory?
A: In a conventional factory, what matters is continuously increasing overall efficiency by using familiar approaches and methods. The objective in an Industry 4.0 factory is exactly the same, namely increasing overall efficiency, but the path to achieving this is different. It principally involves learning from what we see and making the correct future-oriented decisions. New developments offer opportunities for overcoming the existing limits of the ‘old’ world and re-defining overall efficiency – regardless of the discipline, technology, or methods. As Production Manager, it is a matter of learning from new approaches and having the courage to go beyond the limits of the familiar, whereby the new technologies are the prerequisite for actually being able to shift the limits in the first place.
Q: What are the main lessons that you have learned from the factory in recent months?
A: The complexity of a new production system like the one created here poses new challenges for the organization. We have to re-position ourselves organizationally in order to, on the one hand, achieve market-oriented production that meets customer requirements. On the other hand, we must further develop the production system as a whole while integrating new variants. Conventional planning and control systems rapidly come up against their limits.
So, in order to meet these demands, we have introduced agile forms of work which enable us to react considerably more flexibly to the dynamically changing requirements. Our agile teams exploit real-time data, or previously prepared information gained from data-mining processes, to reach decisions in their stand-up meetings and sprints. And the fact is that here, too, we are still only at the beginning and learn something new every day. To return to your original question about the main lessons, we have learned that we must combine technical and organizational innovations in order to act much more rapidly and purposefully, and exploit the new added values.
Q: Can you describe these advantages in more detail?
A: In recent months, for example, we have implemented new products in the production logic. Whereby we already profit from highly automated plants during the prototype phase – without having to manually construct a special plant for the prototypes. And it works! The flexibility of the factory speaks for itself. We produce prototypes parallel to serial production.
Q: How do you achieve this flexibility?
A: Our factory has a modular structure. The individual fully and partially automated production modules are connected to one another via small autonomous carts (AGCs). In contrast to conventional serial production, we can easily run experiments here or simply implement new products. The whole production plant doesn’t immediately come to a standstill if there is a minor problem. This demonstrates pure flexibility. It means that we have a lot less trouble overall when we go through a start-up phase. We work considerably more robustly and have far more freedom.
Q: What happens if a plant breaks down? Can another one simply take over?
A: Yes, that would work. Although we do not have duplicates for everything, we have processes that we can run fully automatically or manually. Whereby the higher-ranking Manufacturing Control System (specially developed for the factory) takes over control of material flows.
Q: Last year, we were talking about five product families in the production process. What is the situation now?
A: We have meanwhile implemented two additional product families – so we now have seven product families in the production process, with two more coming online by the end of the year. The number of variants within these families is also growing. We have implemented a few thousand variants so far. The machines can handle this growth without any trouble. We are even producing both safe and non-safe products on the same modules.
Q: You mentioned data mining earlier. Can you tell us what you have learned about this?
A: We have divided up our production-related data into three main categories. In the smart manufacturing category, we go to the process level to improve quality, increase overall equipment effectiveness, and so on. That is one key issue. The second is the topic of predictive maintenance. We use digital signals here to implement maintenance-related activities as efficiently as possible. We do not always have rigid maintenance cycles – instead, sensors and actuators send a signal if maintenance becomes necessary. The third category involves energy management. We have learnt how much energy the whole hall consumes in a year. In future, this transparency will help us achieve production that is as energy-efficient and sustainable as possible because we can run production when electricity is cheaper.
Q: Can you already draw conclusions from the data in the spirit of Industry 4.0?
A: I have to answer this question with a highly respectful ‘yes and no.’ Yes, we can already draw initial conclusions. And yes, the more we succeed in this, the greater the range of possibilities. A quick example: We digitally monitor compressed air in our production modules. That’s not been done before. We now know that faulty production occurs when the pressure falls below 5 Bar. We now monitor this digitally with warning limits. When these are over- or undershot we trigger a ticket for support via the Bosch Performance Manager (BPM). Another example is the traversing speed of cylinders. One can use this to detect typical signs of wear. This data will help us organize maintenance warning limits for the most varied of actuators and sensors. The aim must be to detect faults and failures before they occur.
Q: Has anything already happened that you would not have discovered without the data?
A: We had a situation in a module where we were monitoring compressed air with SICK’s FTMg sensor. The sensor itself is connected to the cloud via a gateway (TDC-E). We host the BPM – which helps us visualize the data – in the cloud. As a result, we can recognize pulsing of the compressed air supply and take appropriate measures. If the fault had remained undetected it would have led to the failure of a switching valve. We were able to replace it in good time, preventing a machine stoppage.
Q: Does deep learning also play a role in the factory of the future?
A: Absolutely. Deep learning is a technology that can help us improve in various ways. We are currently working on a solution with which we can use neuronal networks in our quality inspections. In concrete terms, this should be an inline-enabled automatic optical inspection (AOI) of solder joints. As you can see, we are learning something new every day and testing new technologies.
Q: Could you complete this sentence for us? The factory of the future…
A: …must be started in the present, otherwise the future will simply remain the ‘perpetual’ future. With the help of data, we can now exploit the opportunities of generating added value – and thus producing as efficiently as possible.